หมอนยางพารา patex เป็น หมอนสุขภาพ นอกจากนี้ หมอนยางพารา สามารถผลิตได้ภายในประเทศ ขอขอบคุณบทความจาก นิตยสารยางเศรษฐกิจ [กดลิ๊ง] ที่พาเราได้ดู โรงงาน หมอนยางพารา นอกจากนี้ ยังขอขอบคุณ ไชยา วรสิงห์ โทรศัพท์ 09-4813-8488
วันนี้ บนเกาะภูเก็ต ของฝากยอดฮิต ต้องซื้อติดมือนักท่องเที่ยวชาวจีน รวมถึงชาติอื่นๆ ไม่ใช่
น้ำพริกกุ้งเสียบ ไม่ใช่พริกแกงไตปลา ไม่ใช่ขนมเต้าส้อ
แต่คือ “ หมอนยางพารา ” สินค้าขึ้นชื่อที่คนไทยเองแทบไม่รู้จัก
เหตุใดชาวต่างชาติ โดยเฉพาะประเทศจีนจึง ฮิต หมอนยางพารา จากประเทศไทย
มิติแรก หมอนที่ผลิตจากยางพารา มีคุณสมบัติ ไม่มีอันตรายจากสารเคมีตกค้าง ไม่มีไรฝุ่น และไม่เป็นแหล่งสะสมของเชื้อโรคที่มาจากฝุ่น สามารถช่วยในการระบายอากาศได้เป็นอย่างดีไม่เกิดกลิ่นเหม็นอับ นุ่มสบาย
หากแต่ราคาในต่างประเทศ เมื่อตีเป็นเงินไทยใบละ ไม่ต่ำกว่า 4,000 บาท
ราคาขนาดนี้ ถ้าไม่รวยจริงซื้อไม่ได้ ขณะที่คนไทยประเทศที่ผลิตยางพารามากที่สุดของโลกก็ยากจะเอื้อมถึง
แต่ไม่กี่ปีที่ผ่านมา ธุรกิจ หมอนยางพารา ถูกติด “ไฮสปีด” ด้านการผลิต สามารถผลิตได้ปริมาณมากขึ้น มีผู้ลงทุนมาก
ราย โดยเฉพาะรายระดับกลางๆ และ ระดับ SME หรือแม้แต่กลุ่มเกษตรกร สาเหตุเกิดจาก การลดลงโรงงานผลิตหมอนใช้เงินลงทุนค่อนข้างสูง จึงมีแต่ผู้ผลิตรายใหญ่ เน้นตลาดส่งออกเป็นหลัก
แต่เมื่อประเทศไทยให้ความสำคัญกับการแปรรูปยางพาราเป็นผลิตภัณฑ์ งานวิจัย หมอนยางพารา ที่ผลิตจากน้ำยางข้น ได้รับการถ่ายทอด และส่งเสริมการผลิต รวมถึงงานวิจัยในการลดต้นทุนการผลิตลง ให้เหมาะสมกับการลงทุนของธุรกิจขนาดเล็ก และกลุ่มเกษตรกร
วันนี้ หมอนยางพารา จึงราคาแค่ 500-600 บาท เป็นสาเหตุให้ชาวต่างชาติที่มาเมืองไทย ต่างหิ้วหมอนกลับประเทศบ้านเกิด กลายเป็นสินค้ายอดฮิตแห่งยุค
ขณะที่คนไทยยังสามารถเป็นเจ้าของได้ไม่ยากนัก
ธุรกิจ หมอนยางพารา จึงมีช่องทางตลาดค่อนข้างสดใส ทั้งในและต่างประเทศ
ขณะที่ภาครัฐที่กำลังเร่งงานส่งเสริมการนำยางพารามาใช้ประโยชน์ในประเทศ ส่วนหนึ่งส่อง “สปอตไลท์” มาที่ธุรกิจนี้ เพราะลงทุนไม่สูงนัก แต่สามารถเพิ่มมูลค่าได้หลายเท่าตัว
เมื่อเทียบเนื้อยางกันกิโลต่อกิโล หมอนยางพารา ได้กำไรกว่าการแปรรูปยางกลางน้ำ ไม่ต่ำกว่า 3 เท่าตัว
จึงไม่แปลกที่ธุรกิจนี้กำลังเติบโตสุดขีดเหมือนได้ “ฮอร์โมน” เร่งชั้นดี ทั้งในภาคเอกชน และที่น่าจับตาคือ ภาคเกษตรกร สามารถเข้าถึงการลงทุนได้ง่าย ผ่านโครงการสนับสนุนของรัฐ ทั้งแบบเงินกู้ดอกเบี้ยต่ำ และเงินลงทุนให้เปล่า โดยมีตลาดต่างประเทศรองรับ
สหกรณ์ฯ ยางหลายแห่ง วันนี้โรงงานผลิตยังไม่เสร็จดี บางแห่งมีแต่อาคารเปล่าๆ รอเครื่องผลิต แต่ตลาดมีออเดอร์รองรับเป็นแสนใบ
นี่คือเรื่องจริง !!!
คำถามก็คือ อุตสาหกรรม หมอนยางพารา ที่กำลังเติบโตสุดขีด มีความสนใจน่าลงทุนมากน้อยแค่ไหน หากจะลงทุนต้องใช้เงินเท่าไหร่ ต้องทำอย่างไรบ้าง และที่สำคัญ ตลาดในอนาคตมีความยั่งยืนมากน้อยแค่ไหน…???
คำถามเหล่านี้จึงเป็นที่มาของการจัดทำสกู๊ปพิเศษ อุตสาหกรรมหมอนยางพารา อนาคต รุ่ง หรือ ร่วงโดยการเสาะหาข้อมูลจากผู้รู้ ผู้เชี่ยวชาญ และกลุ่มเกษตรกรที่ลงทุนธุรกิจนี้ เพื่อสะท้อนให้เห็นภาพ ช่องทาง โอกาส และอุปสรรค อย่างชัดเจนมากที่สุด เนื้อหาทั้งหมดถูกรวบรวมไว้ในสกู๊ปพิเศษฉบับนี้แล้ว
ทีมงานจับเข่าคุย ไชยา วรสิงห์ ผู้เชี่ยวชาญ ด้านการลงทุนอุตสาหกรรมฟองน้ำ และอาจารย์ประจำศูนย์วิจัยวิทยาลัยโลจิสติกส์และซัพพลายเชน มหาวิทยาลัยเทคโนโลยีพระจอมเกล้าพระนครเหนือ
ภาพรวมของอุตสาหกรรมฟองน้ำจากยางพารา และ หมอนยางพารา
ภาพรวมของอุตสาหกรรมฟองน้ำจากยางพารา มีมานานแล้ว แต่ยังไม่ถูกเผยแพร่ ยังมีการเข้าถึงไม่มากนัก ไม่ต่างอะไรกับ “แดนสนธยา”เพราะช่วงแรกๆ การเปิดตัวของอุตสาหกรรมนี้การลงทุนค่อนข้างสูง
เทคโนโลยีการผลิตฟองน้ำจากยางพารา เป็น “โนว์ฮาว” ของภาคเอกชน ไม่มีการเปิดเผยมากเท่าที่ควร
ขณะที่ราคาผลิตภัณฑ์ฟองน้ำจากยางพารา เช่น หมอนและที่นอน ราคาสูง กลายเป็นธุรกิจทำกำไรชั้นดีของเอกชน
ทางด้านหน่วยงานรัฐ แม้จะมีผู้รู้ผู้เชี่ยวชาญหลายท่าน แต่เพราะเครื่องไม้เครื่องมือไม่เพียงพอ จึงไม่ได้รับการถ่ายทอดสู่ภายนอกมากนักมีแค่เครื่องมือเล็กๆ ทำเป็นตุ๊กตา เพื่อจัดนิทรรศการมากกว่า ยังไม่สามารถฉายภาพเชิงพาณิชย์
อีกทั้งความสนใจส่วนหนึ่งของคนในวงการ กระจุกอยู่ที่การแปรรูปยางขั้นกลางน้ำ เช่น ยางแท่ง และยางอัดก้อน เป็นต้น
จนเมื่อปัญหาราคายางเริ่มต้นขึ้นแบบเต็มตัว ภาครัฐจึงหันมาสนับสนุนนโยบายแปรรูปยางเป็นผลิตภัณฑ์มากขึ้น โดยเฉพาะภาคเกษตรกร หน่วยงานภาครัฐจึงต้องมีความเตรียมพร้อมด้านการถ่ายทอดมากขึ้น มีงบประมาณที่จะมาสนับสนุนเครื่องจักรแปรรูปยางพารา ทั้งในรูปของงานวิจัย และเครื่องต้นแบบ
2 ปี ที่ผ่านมา มีการขับเคลื่อนนโยบายแปรรูปยางมากขึ้น รัฐบาลพยายามส่งเสริมเกษตรกรแปรรูปยางเป็นผลิตภัณฑ์ และธุรกิจหมอนยางพารา ได้รับความสนใจ เพราะมีการวิจัยและพัฒนาอุปกรณ์และเครื่องจักรต้นทุนต่ำ สามารถทำได้แบบอุตสาหกรรมขนาดใหญ่และขนาดเล็ก
ขณะที่ตลาดค่อนข้างเปิด เพราะ หมอนยางพารา กลายเป็นสินค้า Best Seller ของนักท่องเที่ยวต่างชาติ
เมื่อภาครัฐมีความพร้อม ตลาดอ้าแขนรับ ประกอบกับภาครัฐมีการส่งเสริม อบรม การผลิตหมอนยางพารา ธุรกิจนี้จึงค่อยถูกคลี่ออก จนกลายเป็นธุรกิจฮิตทำเงินของกลุ่มเกษตรกรในยุคที่ยางราคาตก รวมไปถึงธุรกิจเอกชนขนาดเล็กระดับ SME ก็ลงทุนได้แบบเบาๆ
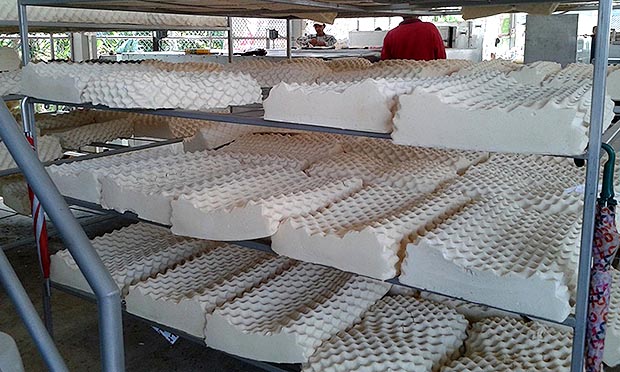
งานวิจัยช่วย ประหยัดการลงทุน หมอนยางพารา
อ.ไชยา บอกว่า เขาเป็นทำงานด้านการออกแบบเครื่องจักรผลิตภัณฑ์ ก่อนจะเข้ามาเป็นหนึ่งในคณะที่ปรึกษาของ นักวิชาการของกรมวิชาการเกษตรในการออกแบบเครื่องมือเครื่องจักร เพื่อการลดต้นทุนการแปรรูปยางพารา เพื่อนำไปถ่ายทอดให้เกษตรกรชาวสวนยาง โดยทำหน้าที่ออกแบบเครื่องจักรให้เหมาะสมกับกระบวนการผลิต ทั้งในมิติของการทำงานและการลงต้นทุน
จึงจำเป็นต้องศึกษาว่าเครื่องจักรที่จะออกแบบนำไปผลิตอะไร ต้องรู้จักวัตถุดิบที่จะนำมาผลิต เรียนรู้ทุกตัวที่เกี่ยวข้อง จึงจะนำมาออกแบบเครื่องจักร และแปรรูปแอบมาเป็นผลิตภัณฑ์
จนเห็นจุดอ่อนของอุตสาหกรรม หมอนยางพารา ที่ลงทุนสูง และเป็นที่มาของการออกแบบให้สามารถลดต้นทุนการผลิตได้อย่างน่าสนใจ
“หลังจากที่ผมศึกษาข้อมูลเครื่องจักรผลิตฟองน้ำ แต่ละประเภท จนพอจะเห็นจุดแข็ง จุดอ่อน ของเครื่องจักรนี้อย่างดี ก่อนจะนำมาประยุกต์ให้เหมาะกับการลงทุน ที่ใช้เงินไม่สูงมากนัก สามารถเข้าถึงการลงทุนอุตสาหกรรมนี้ได้”
ตัวอุปกรณ์ในการผลิตไม่แตกต่างกัน มีถังหมัก เครื่องทำน้ำเย็น (Chiller) เครื่องกำเนิดลม เครื่องฉีดโฟมแบบแม่พิมพ์ ตู้นึ่ง ชุดล้างทำความสะอาดและเตาอบแห้ง
อ.ไชยา บอกว่า เมื่อทำเครื่องจักรผลิตฟองน้ำได้ ตัวสำคัญต่อไปคือ แบบ หรือ โมลด์ (Mould) ที่จะขึ้นรูปเป็นผลิตภัณฑ์ชนิดนั้นๆ เพราะโดยพื้นฐานของเครื่องจักร เคมี และส่วนผสมอื่น จะมีพื้นฐานอยู่ แตกต่างกันเพียงเล็กน้อย ขึ้นอยู่กับว่าจะทำผลิตภัณฑ์ประเภทอะไร ที่เหลือเป็นลูกเล่นของแต่ละโรงงาน
หมอนยางพารา ก็เป็นหนึ่งในนั้น เมื่อก่อนหมอนราคาใบละ 4,000 บาท คนธรรมดาทั่วไป ซื้อได้ยาก ไม่ต้องพูดถึงเกษตรกรที่ผลิตยางพารา เข้าไม่ถึง ทั้งๆ ที่ต้นทุนน้ำยางพารา กก.ละไม่เท่าไหร่
ทำความรู้จัก รูปแบบการผลิตฟองน้ำยางพารา
ในกระบวนการผลิตฟ้องน้ำ ทำได้ 2 ระบบ คือ
ระบบ ทาลาเลย์ (Talalay Process) เป็นกระบวนการผลิตโฟมยางพาราวิธีหนึ่งที่พัฒนาขึ้นขั้นตอนการผลิตมีขั้นตอนทางกลเพิ่มขึ้นคือใส่น้ำยางที่ผสมแล้วเข้าแม่พิมพ์เพียงบางส่วนเสร็จแล้วดูดเอาอากาศในแม่พิมพ์ออก น้ำยางที่ผสมสารเคมีแล้วจะพองตัวขึ้นจนเต็มแม่พิมพ์ แช่แข็งด้วยความเย็น อบด้วยความร้อนนำออกจากแม่พิมพ์ ล้างทำความสะอาดและอบให้แห้ง
ระบบ ดัลลอป (Dunlop Process) เป็นกระบวนการผลิตยางพาราด้วยกระบวนการทางเคมีใช้กับยางพาราธรรมชาติ 100% โดยใช้สารเคมีทำให้ยางพาราเกิดฟองอากาศแทรกตัว โดยใช้เครื่องตีอย่างง่าย เนื้อยางจะค่อยขึ้นตัว เป็นครีมเหลวคล้ายวิปปิ้งครีมจากนั้นนำไปเทลงแม่แบบ ขึ้นรูปจนเต็มอบด้วยความร้อนจนยางสุก นำออกจากแม่แบบนำเข้ากระบวนการล้างสารเคมีออกไม่มีกลิ่นเหม็นของสารเคมีและอบให้แห้ง
“การทำฟองน้ำระบบนี้ ต้องอาศัยความชำนาญ ต้องการควบคุมความหนาแน่น (Density) ยิ่งค่าสูง หมอนจะแข็ง การทำต้องอาศัยความชำนาญ ว่าโฟมขึ้นสูงขนาดใหญ่จึงจะพอเหมาะ
“แต่การลงทุนไม่สูงนัก ต้นทุนไม่ถึง 1 ล้านบาท ผลิตได้วันละ 50 ใบ 1 ปี หากทำงาน 300 วัน จะผลิตหมอนได้ 15,000ใบ บวกกำไรลูกละ 100 บาท จะได้กำไร ปีละ 5 แสนบาท”
การทำหมอนยางพารา ด้วยเครื่องจักรขนาดเล็ก แบบดัลลอบ ประกอบด้วย
- ชุดเก็บสารเคมี มีมอตอร์และถังเก็บ อย่าให้เคมีตกตะกอน
- ถังบ่ม ทำหน้าที่ เก็บน้ำยางและมีชิลเลอร์ (Chiller)หรือเครื่องผลิตน้ำหล่อเย็นมีถัง 2 ชั้น ชั้นใน เป็นน้ำยางข้น ใช้นอกเป็นน้ำเย็น คุมอุณหภูมิให้ได้ 18 องศา จะขึ้นรูปได้ง่าย อุณหภูมิห้องไม่เหมาะ
- ชุดตีโฟม
- โมลด์หรือ แม่แบบ 16 ตัว
- ตู้นึ่ง แบบแก๊ส หรือ ฮีตเตอร์ สามารถตั้งทำงานอัตโนมัติ 2 ตู้
- ชุดล้างทำความสะอาด
- ชุดอบแห้ง ระบบปิด ฮีตเตอร์ พัดลมเป่าลมร้อน 70 องศา
ระบบนี้ ชาวบ้านเกษตรกรสามารถทำได้
ลงทุนเพียง 8-9 แสนบาทเท่านั้น
แม่แบบ ต้นทุน สำคัญ ของอุตสาหกรรมหมอนยางพารา
เมื่อมาเจาะรายละเอียดของการลงทุน พบว่า ต้นทุนที่สำคัญของการทำโรงงานหมอนคือ โมลด์ ซึ่งมี 2 รูปแบบตามประเภทเครื่องจักร
แบบที่ 1 เครื่องจักรประเภทอบไอน้ำ (Steam)เป็นระบบที่ทำให้สุก ด้วยไอน้ำ สมัยก่อนจะใช้โมลด์ที่ทำมาจากอลูมิเนียม หรือ สแตนเลส ซึ่งเป็นวัสดุที่มีมูลค่าสูง ต้องทำการหล่อ เป็นชิ้นเดียว น้ำหนักมาก แต่ข้อดีอายุการใช้งานทนทาน เพียงแต่การลงทุนครั้งแรกสูงมาก
แม่แบบ ของเครื่องจักรอบไอน้ำ น้ำหนักประมาณ 40 กก. ต้นทุนตัวละ 30,000-40,000 บาท ถ้าต้องมีโมลด์ 400 ตัว จะต้องลงทุนประมาณ 14 ล้านบาท
“ถามว่าทำไมจึงต้องมี 400 ตัว เพราะกระบวนการผลิตต้องหมุนเวียนโมลด์ผลิต ครั้งหนึ่งใช้เวลาอบ 25-30 นาที เมื่ออบเสร็จต้องแกะ รอให้โมลด์เย็น ล้าง ต้องใช้เวลา เพราะโมลด์ที่เป็นโลหะสแตนเลส รับความร้อนช้า คลายความร้อนช้า จึงจำเป็นต้องมีเยอะเพื่อหมุนเวียนให้เพียงพอต่อกำลังการผลิตใน 1 วัน”
อีกปัจจัยหนึ่งคือ เรื่องของ รูปแบบ รูปทรงผลิตภัณฑ์หมอน ต้องมีหลากหลาย และต้องมีการเปลี่ยนรูปทรงอย่างต่อเนื่อง เมื่อเปลี่ยนแบบใหม่เพื่อให้ทันสมัยจึงต้องลงทุนโมลด์ใหม่
นี่จึงเป็นคำตอบว่าทำไม หมอนยางพารา จึงราคาสูง ส่วนหนึ่งอยู่ที่การลงทุน ค่าเสื่อมสภาพ เป็นต้น
แบบที่ 2 คือ ระบบ RF (Radio frequency)การทำงานของเครื่องจักรรูปแบบนี้จะเป็นการแลกเปลี่ยนประจุไฟฟ้า เพื่อให้เกิดความร้อนคลายๆกับไมโครเวฟ แต่ความร้อนจะน้อยกว่า
การทำงานเหมือนกับนำอาหารเข้าไปอุ่นในไมโครเวฟ ทำให้สามารถอบในเวลารวดเร็ว ทำให้สามารถผลิตได้วันละมากๆ ใช้เวลาอบ 12-16 นาที เร็วกว่าระบบอบไอน้ำ
ก่อนหน้านี้ระบบนี้จะใช้ในการอบแห้ง เช่น การผลิตเส้นด้าย แต่เมื่อนำมาทำหมอนที่เป็นลักษณะโฟมหรือฟองน้ำ ถ้าไม่มีน้ำเข้าไปอยู่ในกระบวนการอบ จะมีผลต่อโครงสร้างของผลิตภัณฑ์
ข้อดีของระบบนี้คือ อบได้เร็ว แต่ความยากคือ ต้องคำนวณอุณหภูมิการอบให้พอเหมาะ ในกระบวนการอบ สูตรผสมเคมีต้องลงตัวพอดี การอบต้องคำนวณอุณหภูมิอย่างดี ต้องเช็กค่าการขยายตัวของยาง ต้องมีความแม่นยำ เพราะถ้าออกจากเครื่องอบ แล้วไม่สุกไม่สามารถนำมาอบใหม่ได้ ถ้าไม่สุก เวลาแว็กซ์คั่ม จะไม่คืนตัว
ประเด็นสำคัญก็คือ ในกระบวนการอบของระบบนี้ ใช้โมลด์ที่ทำจากโลหะไม่ได้ จะเกิดการลุกไหม้ (Spark) โมลด์จึงต้องเป็นพลาสติกหรือเซรามิก
แต่โดยทั่วไป จะใช้พลาสติก มีต้นทุนตัวละ 8,500-10,000 บาท ถ้ามี 400 ตัว ใช้เงินต้นทุน 4ล้านบาท
จุดอ่อน ก็คือ โมลด์เป็นพลาสติก เมื่อถูกความร้อนเป็นเวลานานๆ จะทำให้เกิดการเสื่อมและแตก อายุการใช้งานประมาณ จึง 2,500-3,000 ครั้ง ต้องเปลี่ยนโมลด์ปีละ 2 เท่ากับจะต้องลงทุนโมลด์ ปีละ 8,000,000บาทอย่างนี้ไปเรื่อยๆ ทุกปี ถ้าทำ 5 ปี เท่ากับว่าลงทุนโมลด์ไปทั้งสิ้น 32 ล้านบาท
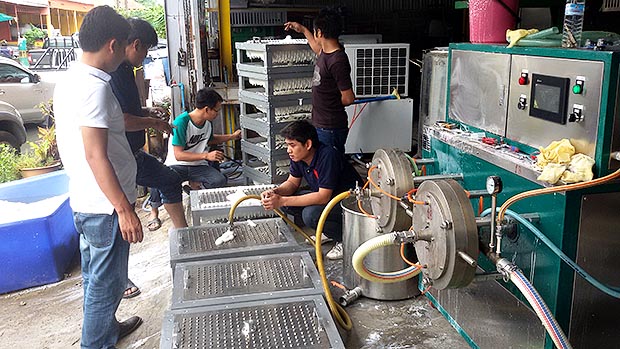
โมลด์ อลูมีเนียม + พลาสติก ปฏิวัติการลงทุนหมอนยางพารา
เมื่อแม่แบบ คือ ต้นทุนหนักอึ้งของ อุตสาหกรรมหมอนยางพารา หลังจากนั้น อ.ไชยา จึงมาหาวิธีลดต้นทุนโมลด์ โดยใช้วิธีผสมผสานระหว่างอลูมิเนียมกับพลาสติก ก่อนจะออกแบบโมลด์โครงเป็นอลูมิเนียม และไส้ในเป็นแบบพลาสติก เพื่อลดต้นทุนลง โดยใช้กับเครื่องระบบ อบไอน้ำ
แน่นอนว่าพลาสติกต้องเปลี่ยนทุกๆ 3,000 ครั้ง แต่โมลด์ชนิดนี้ ไม่จำเป็นต้องเปลี่ยนทั้งชุด แต่เปลี่ยนเฉพาะพลาสติก ส่วนโครงอลูมิเนียมยังใช้ได้เหมือนเดิม
โมลด์แบบนี้ยังสามารถเปลี่ยนรูปแบบโปรดักส์ได้ง่าย เพียงแค่เปลี่ยนพลาสติกเท่านั้น ไม่ต้องเปลี่ยนยกชุด โครงใช้ตัวเดิม
การลงทุน โมลด์อลูมิเนียมกับพลาสติกลงทุนครั้งแรก 15,000 บาท/ตัวลงทุน 400 ตัว เป็นเงิน 6 ล้านบาท ใน 1 ปีจะต้องเปลี่ยนพลาสติก 1,500 บาท/ชิ้นรวมครั้งละ 6 แสนบาท หรือ 1.2 ล้านบาท/ปี
ใน 5 ปี ลงทุนโมลด์ เพียง 5 ปี ลงทุน 11.4 ล้าน
ข้อดี ของโมลด์รูปแบบนี้ คือ ยืดหยุ่นปรับเปลี่ยนโมลด์ได้ ไม่ต้องเปลี่ยนทั้งชุด
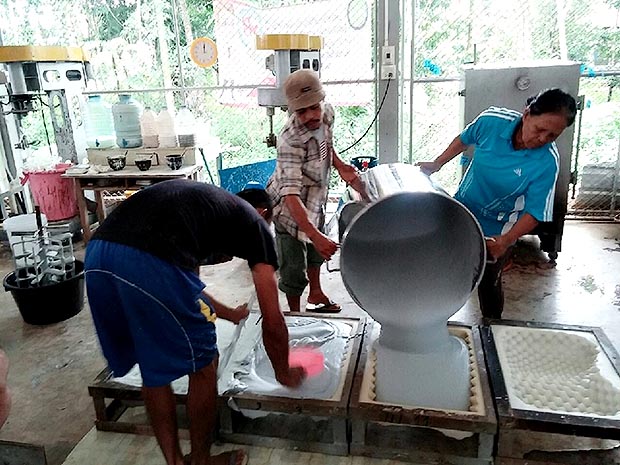
เมื่อลงทุนลดลง ผลิตภัณฑ์ราคาลดลง
ในอดีต ชาวสวนยาง เป็นผู้ผลิตวัตถุดิบ น้อยคนที่จะได้นอน หมอนยางพารา ก่อนหน้านี้ราคา 4,000 ปัจจุบัน 500 ก็ซื้อได้แล้ว
วันนี้พื้นที่ปลูกยางพารามีทั่วประเทศ และราคากำลังตกต่ำอย่างหนัก เมื่อยางมีเยอะเราต้องนำยางมาแปรรูป เพิ่มมูลค่า นำมาใช้ในชีวิตประจำวัน และฟองน้ำอยู่ในชีวิตประจำวันของเรา
วันนี้เมื่อต้นทุนถูก ราคาผลิตภัณฑ์ก็จะต่ำไปด้วยเพราะปกติการคิดค่าเสื่อมราคา จะนำมาคำนวณในราคาสินค้า
สมมุติผลิตวันละ 1,000 ใบ ปีละ 300 วัน ปีละ 3 แสน ทำงาน 5 ปี เท่ากับ 1.5 ล้าน หากลงทุน 25 ล้าน ต้นทุนค่าเสื่อมราคา 16 บาท/ลูก
แต่ถ้าลงทุน 50 ล้าน ต้องคูณสอง คือ 32 บาท/ใบ ค่าพลังงาน ค่าจัดการ วัตถุดิบ จากนั้นคิดการตั้งกำไรกี่เปอร์เซ็นต์ จนกลายมาเป็นราคาขาย
เมื่อหมอนราคาถูกลง คนก็หันมาใช้กันมากขึ้น เพราะปัจจุบันคนไทยหันมาใส่ใจเรื่องสุขภาพ การนอนก็เป็นหนึ่งในนั้น หมอนยางพาราเป็นหมอนเพื่อสุขภาพ นิ่ม ไม่มีไรฝุ่น ไม่เป็นอันตรายกับผู้เป็นโรคภูมิแพ้ และยังตอบโจทย์รัฐบาลในการเพิ่มการใช้ยางพาราในประเทศ เพื่อมูลค่ายางพารา
หมอนยางพาราตอบโจทย์วิกฤติราคายางอย่างดี
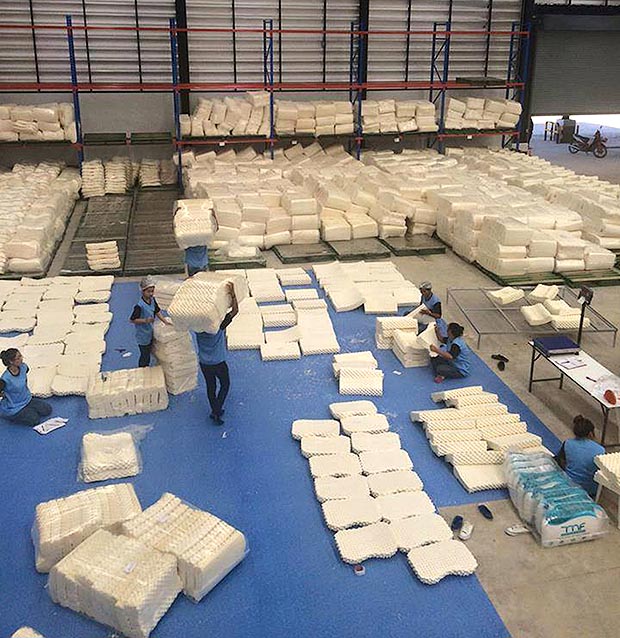
อุตสาหกรรมฟองน้ำยางพารากว้างเหมือนทะเล
การทำฟองน้ำ ตามคำแนะนำของ อ.ไชยา จะบอกเสมอว่า ไม่จำเป็นต้องทำเป็นหมอนอย่างเดียว แต่ทำอะไรก็ได้ที่เป็นฟองน้ำ ทำเป็นแผ่นรองนั่ง อาศนะพระ พรมปูละหมาด หรือ ที่นอนพับ เบาะนั่งจักรยาน เบาะมอเตอร์ไซค์ เบาะรถยนต์โซฟา อะไรก็ได้ที่แทนฟองน้ำ เพราะมันขึ้นอยู่กับแบบว่าจะทำอะไร เพราะทุกวันนี้ฟองน้ำอยู่ในชีวิตประจำวันของเรา
ถ้าไปทางภาคอีสาน จะเห็นว่าแต่ละบ้านมีหมอนหนุนขนาด 3 เหลี่ยม หรือเรียกว่า “หมอนขิด” จะมีเกือบทุกบ้าน มีที่นอนแบบพับ แต่ละบ้านมีเยอะมาก หมอนขิด ใช้แจกตามงานสำคัญทางศาสนา และพิธีต่างๆ สามารถทำได้แทนการใช้นุ่น
หอพักที่เป็นที่นอนปิกนิก เก็บพับง่าย ที่นอนในโรงพยาบาล ฟองน้ำยางพาราจึง ใช้แทนนุ่น และฟองน้ำเคมี
ผลิตหมอนยางพารา ต้นทุนต่ำ ตลาดเปิดกว้างทั้งในและนอก
การลงทุนทำฟองน้ำยางพาราไม่ยาก แต่ต้องเรียนรู้เรื่องการทำฟองน้ำให้เชี่ยวชาญก่อน ทางสถาบันวิจัยยางมีการเปิดอบรมหลักสูตรการทำฟองน้ำ อย่างสม่ำเสมอ สามารถติดต่อไปได้ มีการเรียนการสอนทฤษฎี ปฏิบัติ 3 วันเท่านั้น
ส่วนเรื่องเครื่องจักร ราคามีถูกมีแพง มาดูตัวอย่างแล้วส่วนไหนที่คิดว่าหาหรือทำได้ถูกกว่า ก็เลือกซื้อเลือกทำเป็นชิ้นๆ เพื่อจะลดต้นทุน จากนั้นค่อยลงทุน ไม่ใช้ลงทุนเครื่องแล้วค่อยมาเรียนรู้
“เมื่อทำฟองน้ำเป็น ไม่แนะนำให้ทำหมอนอย่างเดียว ย้ำว่าทำอะไรก็ได้ ที่เป็นฟองน้ำที่ทำจากปิโตรเลียม”
อ.ไชยาบอกว่า วันนี้ถ้าผู้ผลิตหมอนยางพาราไม่เอากำไรเยอะ โตแน่นอน เพราะหมอน คนไม่ได้ใช้เฉพาะกลางคืน ในรถก็มีหมอน ที่ทำงานก็มีหมอน มีผลิตภัณฑ์กว้างเป็นทะเล คือ ฟองน้ำทั้งหมดใช้ยางพาราแทนได้หมด อยู่ในทุกๆ ที่ในชีวิตประจำวันของเรา
“ประเทศไทยมีประชากร 60 ล้าน มีความสามารถซื้อหมอน 30 ล้านคน แล้วทำราคาให้ต่ำกว่า 500 บาท ตลาดจะกว้างขนาดใหญ่ ถ้ามี 100 โรง 23 ปี กว่าจะผลิตป้อน 30 ล้านคน นี่แค่ในประเทศ
“บ้านเราตอนนี้มีไม่ถึง 10 สหกรณ์ที่ทำ เอกชนประมาณ 10 โรงบริษัทเอกชนใหญ่ จะไม่ผลิตขายในประเทศ แต่จะเน้นส่งออกเป็นหลัก แต่สหกรณ์เอากำไร 50 บาท ใบละ 300 บาท แต่ปริมาณเพิ่มขึ้น
“ตอนนี้สามารถลดต้นทุนได้ กำลังการผลิต 300-400 ใบ ระบบปิด เครื่องฉีดโฟมจากเยอรมัน ทำได้ไม่เกิน 15 ล้านบาท จากเดิม 25 กว่าล้าน ไม่รวมอาคาร มีติดต่อมาแล้ว 7 สหกรณ์ในภาคใต้”
ที่น่าสนใจก็คือ การลงทุนผลิตหมอนของชุมนุมสหกรณ์กองทุนสวนยางบึงกาฬที่ออกแบบโรงงานต้นแบบในการแปรรูปยางพาราแบบยั่งยืน เน้นการผลิตครบวงจรตั้งแต่ต้นน้ำ กลางน้ำจนถึงปลายน้ำ โดยได้รับการสนับสนุนทั้งภาครัฐและเอกชน จากชัยภูมิที่ลงตัวด้านการขนส่งตามแผนขยายการขนส่ง R12 จึงเป็นต้นแบบการลงทุนของสหกรณ์ที่น่าสนใจและน่าศึกษาเป็นแบบอย่างของสหกรณ์ทั้งประเทศที่จะไปศึกษาดูงาน
นอกจากนั้น อ.ไชยากำลังสร้างเครื่องต้นแบบผลิตน้ำยางข้น แบบชุดครีมมิ่ง (Creaming) ชาวสวนสามารถนำน้ำยางสดมาเข้าเครื่องเพื่อผลิตน้ำยางข้นแล้วแปรรูปได้เลย เป็นระบบที่เหมาะกับชาวสวนยางที่อยู่หางไกลโรงงานน้ำยางข้น สามารถเพิ่มมูลค่ายางพาราไทยได้ทั่วถึงและยังยืน เป็นการช่วยชาวสวนยางที่กำลังเดือดร้อนเรื่องราคายางพาราที่ตกต่ำในปัจจุบันให้สามารถแปรรูปยางพาราเพื่อเพิ่มมูลค่าได้อย่างครบวงจร “ ไทยทำไทยใช้ “
ขอขอบคุณ
ไชยา วรสิงห์
โทรศัพท์ 09-4813-8488, 06-3179-5308